The wood remains among the primary materials used for construction. From framing and finishing to the final stage it is a key part in a variety of construction projects. One of the most crucial methods of working with wood is the takeoff, a complete analysis, and estimation of the total amount of wood components required to complete an undertaking. Making sure that the wood is taken off accurately provides an excellent foundation for plan, budgeting, and execution. This allows contractors to anticipate requirements as well as reduce the amount of waste that is generated and avoid expensive project delays.
This article examines the significance of wood takeoffs, the essential elements in the procedure, strategies for making sure precision is maintained, as well as the perfect techniques that result in the success of the project.
The Importance of Wood Takeoffs
Wood takeoffs are the initial step to estimate the cost, sourcing, and the wood material definitely. It is the process of quantifying each piece of wood required for the construction process starting from structural support and beams to finished carpentry components. An extensive takeoff gives an understanding of the amount size, shape, and cost of Lumber Takeoff services. A precise wood takeoff can bring substantial benefits to construction management such as the control of costs, efficient scheduling, and the allocation of resources.
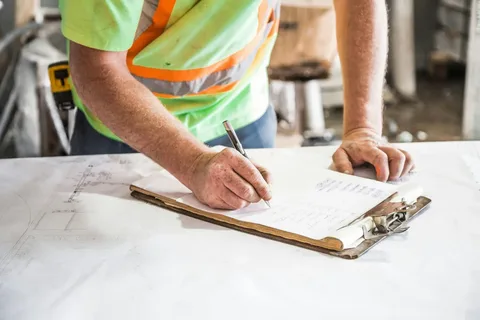
Cost Control and Budgeting
Wood takeoffs provide an essential element to the budget. With accurate estimates of the quantities and kinds of wood required contractors are able to create real-world budgets and distribute budgets in the right way. If takeoffs aren’t precise budgets could be incomplete which can lead to unplanned expenses or unnecessary excesses, as well as problems with logistics that can affect profits. Lumber takeoffs provide the necessary information on costs for materials and are essential to creating a precise and accurate project budget.
Resource Management
Being aware of the amount of wood that will be required allows project leaders to source materials with the least amount of loss. This helps to reduce costs that are not needed but also reduces the environmental footprint of a project. Effective use of material can reduce the necessity for last-minute orders, which could cause delays to projects and more cost. In addition, taking offs that are well-planned can assist contractors in coordinating with their suppliers to warrant timely delivery that keeps projects moving forward.
Scheduling and Labor Efficiency
Wood takesoffs can also aid in the efficient scheduling of projects. With the exact quantity of the materials required contractors are able to organize their the resources of labor better definitely. Employees can concentrate on their assigned projects without having to look for extra supplies, thus avoiding any interruptions. This helps not only shorten the timeline of projects but also helps keep the cost of labor in line with the budget.
Key Components of a Wood Takeoff
The process of executing a successful wood takeoff requires more than just listing the items. The process is meticulous which includes the calculation of quantities and waste elements and the material’s specifications. Every component is essential to warrant accuracy and support the efficient execution of projects.
1. Quantifying Material Needs
The precise measurement of wood requirements is vital to create the most reliable takeoff. It is necessary to measure the 2×6 actual Size as well as the area and volume of every wood component required for the undertaking. Based on the nature of the work that could involve estimating the quantities needed for flooring, framing as well as cabinetry and trim. Every type of wood has its own needs for construction which is why quantifying the needs of each permits precise planning and budgeting.
2. Accounting for Waste Factors
In any construction venture, however, it can be reduced with carefully planned preparation. Things like loss of cutting, wood defects as well as material handling should be considered in the taking off so that there are no under-estimations. The accounting for waste permits contractors to purchase a surplus to cover potential losses usually between 10 and 20%, contingent on the size of the work. Inadequately assessing waste could cause material shortages as well as more charges for additional orders.
3. Specifying Wood Types and Grades
Certain parts of projects might require various types or varieties of wood, based on the structural needs aesthetic appeal, and endurance. For instance, structures that are designed to carry loads might require hardwoods, whereas ornamental features may require more softwoods. By indicating these requirements in the start-up phase ensures that the appropriate products are selected for each element of the plan to avoid compatibility and difficulties with performance.

Methods and Tools for Accurate Wood Takeoffs
Many methods are available for fulfilling exact takeoffs from wood. Depending on the scope and difficulty of the task certain contractors use traditional methods of manual labor, whereas others employ advanced instruments to increase accuracy and efficacy.
Manual Takeoffs
For projects that are smaller or less complex taking offs by hand can prove efficient. This involves the creation of detailed lists of materials for wood that are based on blueprints or other physical measures. However, taking offs by hand could be lengthy and raise the chance of human errors. They require focus on detail and usually require calculating lengths, dimensions, and the size of areas manually. Although labor-intensive manual takeoffs aren’t the most efficient, they are cost-effective for smaller assignments or for situations where the digital resources available are insufficient.
Digital Takeoff Software
The digital takeoff program has changed how woodworkers approach takeoffs. Software such as AutoCAD, Bluebeam, and PlanSwift permit contractors to execute takeoffs together with digital blueprints, producing dimensions, amounts, and prices instantly. They allow users to enter particular measurements and calculate automatically numbers, dramatically decreasing the chance of making mistakes. In addition, many of these tools work with management tools for projects to streamline planning, ordering, and planning.
Building Information Modeling (BIM)
Large-scale projects require large-scale models. Building Information Modeling (BIM) platforms prepare the highest level of precision and coordination. BIM platforms generate a complete 3D representation of the project that incorporates all structural components which includes wood components. This is not just helpful in the quantification of materials but gives a visual representation of the design, which allows all people to review the project at any time. BIM allows for the flexibility of adjusting the measurement and quantity of materials when changes take place, making sure that the takeoff is accurate and current throughout the entire project.
Leading Practices for Effective Wood Takeoffs
Affirming accurate techniques is vital to making accurate and reliable wooden takeoffs. The accurate practices assure that the materials used in wood are precisely measured and that the takeoff is an enduring base for your project.
Collaboration in conjunction with Design and Engineering Teams
A close collaboration between the engineers and design teams will ensure that the wood takeoffs are in line with the specifications and structural requirements of the design. Any modifications in the design could impact the material requirements, therefore collaboration with other stakeholder groups permits timely modifications at the time of takeoff.
Recheck Measurements and Calculations
Inaccurate measurements or calculations may result in incorrect takeoffs that disrupt budgets and timeframes. Before approving the takeoffs check measures and calculations to ensure accuracy. This is particularly important in large-scale projects, where even small deviations can have major financial consequences.
Factor in Seasonal Wood Variability
Wood is a natural substance that expands and contracts in response to temperatures and moisture. It is important to factor this variability into the decision-making process, especially when working in areas that experience significant fluctuations in the seasons. Kiln-dried, seasoned, or dried wood eliminates the risk of this, however, adjustments might be required to accommodate expansion or contraction.
Use Clear, Detailed Documentation
A thorough documentation will ensure that team members are aware of the wood needs. Comprehensive descriptions of different types of wood and grades, measurements, and amounts facilitate the process of procuring and reduce miscommunication, which can be particularly beneficial in dealing with suppliers.
Conclusion
A thorough wood takeoff is vital for the success of building projects. It gives an outline of materials procurement, budgeting, as well as scheduling. It doesn’t matter if you’re together either manual or electronic equipment, contractors gain exact takeoffs which prevent the waste of materials, reduce costs, and speed up the process of executing projects. If they adhere to excellent methods and use the appropriate equipment, project managers will be able to warrant that takeoffs made from wood are efficient, sustainable, as well as cost-effective construction.