Compressed air systems are essential in many industries, powering tools, machinery, and various processes. However, for these systems to operate efficiently, maintaining clean, dry, and contaminant-free air is critical. This is where compressed air filter come in—they remove particles, moisture, and oil from the air to ensure it remains pure.
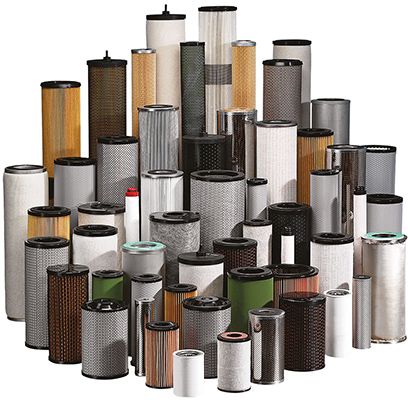
Over time, however, compressed air filters can encounter problems that affect performance and overall system efficiency. In this article, we’ll explore some of the most common problems with compressed air filters and provide practical solutions to help keep your system running smoothly.
Table of Contents
Sr# | Headings |
---|---|
1 | What is a Compressed Air Filter? |
2 | Importance of Maintaining Compressed Air Filters |
3 | Common Problems with Compressed Air Filters |
4 | 1. Clogging or Blockage of Filter |
5 | 2. Oil and Water Contamination |
6 | 3. Leaking Compressed Air Filters |
7 | 4. Pressure Drop Across the Filter |
8 | 5. Inconsistent Airflow |
9 | How to Fix Common Compressed Air Filter Problems |
10 | Regular Inspection and Maintenance |
11 | Choosing the Right Compressed Air Filter |
12 | When to Replace Your Compressed Air Filter |
13 | Conclusion: Keep Your System Clean and Efficient |
What is a Compressed Air Filter?
A compressed air filter is a device used in air compressor systems to remove contaminants such as dust, dirt, oil, and moisture from compressed air. Clean, dry air is necessary to ensure the proper functioning of air-powered tools, machinery, and even the system itself. Filters are usually placed at various points in the compressed air system to ensure that the air remains free from harmful substances.
Without proper filtration, contaminants can damage sensitive equipment, reduce the efficiency of tools, and even lead to costly repairs. Regular maintenance of air filters ensures that your system operates smoothly and that the air quality remains optimal for your applications.
Importance of Maintaining Compressed Air Filters
Maintaining your compressed air filters is crucial for preventing system malfunctions and ensuring the long-term reliability of your compressed air equipment. Over time, filters can become clogged or contaminated, leading to issues like decreased efficiency, increased energy consumption, and higher operational costs.
Regularly inspecting and servicing your filters will not only improve air quality but also extend the life of your compressor and associated equipment. Neglecting filter maintenance can lead to expensive repairs, system downtime, and productivity losses.
Common Problems with Compressed Air Filters
Even with regular maintenance, compressed air filters can experience a range of issues that compromise the quality of the compressed air. Below are some of the most common problems with compressed air filters and how to address them:
1. Clogging or Blockage of Filter
One of the most common issues with compressed air filters is clogging. Filters are designed to capture contaminants, but over time, dirt, dust, and other particles can accumulate and block the filter. When this happens, air flow is restricted, reducing system efficiency and potentially causing system pressure issues.
Solution:
Regularly inspect and clean the filter. Depending on the type of filter, it may be necessary to replace it if it has become too clogged. For reusable filters, cleaning them with compressed air or a soft brush can help restore airflow. For non-reusable filters, timely replacement is essential.
2. Oil and Water Contamination
Despite filters being designed to remove oil and water, certain situations can lead to excessive moisture or oil contamination in the system. If the compressor’s air intake is pulling in air with a high moisture level or oil-laden air, it can overwhelm the filter’s ability to remove contaminants effectively. This can cause issues like corrosion, rust, or sludge build-up in the system.
Solution:
Ensure that your system is equipped with proper moisture and oil separators in addition to the air filter. If oil or water contamination is an ongoing problem, check the compressor for leaks or malfunctions in the separator. In some cases, you may need to upgrade to a higher-quality filter designed to handle greater levels of moisture or oil.
3. Leaking Compressed Air Filters
Air leaks around the filter housing or connections are another common issue. Leaks can occur due to poor installation, aging seals, or physical damage to the filter housing. Leaks not only reduce the efficiency of your air system but also lead to wasted energy and higher operational costs.
Solution:
Inspect the filter and its housing for any signs of damage or wear. Check the seals to ensure they are intact and fit properly. If you find any cracks, replace the damaged parts immediately. Proper installation and periodic checks can prevent leaks from becoming a significant issue.
4. Pressure Drop Across the Filter
A pressure drop across the filter is a common issue that occurs when the filter becomes clogged or too dirty. When this happens, the system has to work harder to push air through the filter, leading to lower output pressure and reduced efficiency. A significant pressure drop can cause downstream equipment to malfunction or underperform.
Solution:
If you notice a pressure drop, it’s time to clean or replace the filter. Some advanced filters come with built-in pressure gauges that can alert you to pressure loss, making it easier to detect when maintenance is needed. If pressure drops persist even after cleaning or replacing the filter, inspect the system for additional blockages or restrictions in the airflow path.
5. Inconsistent Airflow
Inconsistent airflow from the compressed air system can be caused by a variety of issues, including clogged filters, improperly sized filters, or issues with the compressor itself. If the airflow is erratic, tools may not function properly, and equipment could be underpowered.
Solution:
Check the filter for signs of clogging or contamination. If the filter is in good condition, consider whether the filter size is appropriate for your system. If your system requires a higher flow rate, upgrading to a larger or higher-capacity filter could help maintain a steady airflow.
How to Fix Common Compressed Air Filter Problems
Here are some tips to help you address common issues with your compressed air filters:
- Regularly inspect your filters: Make it a habit to check the filters at regular intervals. This will help you catch issues before they become major problems.
- Clean filters when needed: For reusable filters, make sure to clean them regularly to maintain airflow. For disposable filters, replace them according to the manufacturer’s recommendations.
- Check for leaks: If you suspect an air leak, inspect all seals and connections around the filter. Replace any damaged parts immediately.
- Upgrade filters if necessary: If your filters aren’t handling your system’s demands, it may be time to invest in higher-quality or larger filters that can handle greater volumes of air or more severe contaminants.
- Use oil and moisture separators: Adding moisture and oil separators before the filter can help reduce the load on the filter and improve air quality.
Regular Inspection and Maintenance
Regular inspection and maintenance are critical to keeping your compressed air system running smoothly. Be sure to:
- Check filters for dirt, moisture, and oil build-up.
- Replace or clean filters according to the manufacturer’s recommendations.
- Inspect all seals and connections to prevent air leaks.
- Monitor system performance to detect any signs of inefficiency or pressure loss.
A well-maintained filter will not only extend the life of your equipment but will also improve air quality, reduce energy costs, and prevent costly downtime.
Choosing the Right Compressed Air Filter
Choosing the right filter is key to avoiding problems down the line. When selecting a compressed air filter, consider:
- Flow rate: Ensure the filter matches the air flow requirements of your system.
- Filtration level: Different applications may require different filtration levels (e.g., fine filters for sensitive tools or equipment).
- Environmental conditions: Consider the operating environment. If your system is exposed to high humidity or oil-laden air, choose a filter that is designed to handle these conditions.
Consult with a professional or a reputable filter manufacturer to ensure you select the best filter for your system.
When to Replace Your Compressed Air Filter
Even with regular maintenance, filters don’t last forever. Signs it’s time to replace your filter include:
- Persistent air quality issues despite cleaning or replacing parts.
- A significant pressure drop that cleaning or adjusting the filter doesn’t fix.
- Physical damage to the filter housing or seals.
Always follow the manufacturer’s guidelines for filter replacement and choose high-quality replacements to ensure continued system performance.
Conclusion: Keep Your System Clean and Efficient
Compressed air filters play a vital role in maintaining the quality and efficiency of your compressed air system. By addressing common problems like clogging, contamination, leaks, and pressure drops, you can keep your system running smoothly and avoid costly repairs. Regular inspection, cleaning, and replacement of filters, along with choosing the right type for your needs, will ensure that your system continues to operate at peak performance. read more
FAQs
1. How often should I clean or replace my compressed air filter?
The frequency depends on your system’s usage and the environment. Typically, filters should be inspected every 3 to 6 months, with cleaning or replacement as needed.
2. Can I repair a damaged compressed air filter?
If the filter housing or seals are damaged, it’s usually best to replace the entire filter. Small issues like dirt accumulation can often be cleaned.
3. What happens if I don’t maintain my compressed air filter?
Failing to maintain your filter can lead to contaminated air, reduced system efficiency, equipment damage, and increased energy costs.
4. Can oil contamination be removed by compressed air filters?
Yes, oil can be removed by filters specifically designed for oil removal. However, if the oil contamination is severe, additional separators may be required.
5. Why is there a pressure drop after installing a new filter?
A pressure drop could be due to the new filter being too restrictive or not properly installed. Ensure the filter is sized correctly for your system and check for installation errors.